Products
Application
Available in different sizes (12" x 12" clear opening to 48" X 48" clear opening) and load ratings (A15 to F900), our range of manhole covers are ideally suited for different types of important applications.
Why Crescent Foundry?
Since 1982, Crescent has been pushing the boundaries of innovation in the field of foundry solutions. With multiple state-of-the-art production facilities, we rank among the largest, globally recognised cast iron solution providers from India.
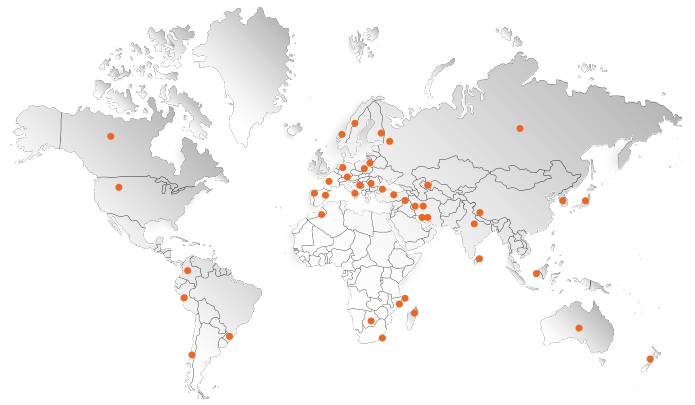
Infrastructure
World-class production facilities with cutting-edge machinery and advanced, digitised operations.
Infrastructure
World-class production facilities with cutting-edge machinery and advanced, digitised operations.
-
Process
- High Pressure Moulding
- Semi Automatic Moulding
- Vacuum Moulding
- Lost Foam Moulding
-
Process
- High Pressure Moulding
- Semi Automatic Moulding
- Vacuum Moulding
- Lost Foam Moulding
-
Facilities
- Floor Moulding And Jolt and Squeeze
- High Pressure Moulding
- Vacuum Moulding
- Fabrication
- Testing
- Others
Quality & Certification
Several prestigious product and process certifications bear testimony to the quality standards we adhere to at every stage.
Place Enquiry
Get in touch with us today to place an enquiry for our top-quality castings and industrial products.