The value of the worldwide forklift market stood at around…
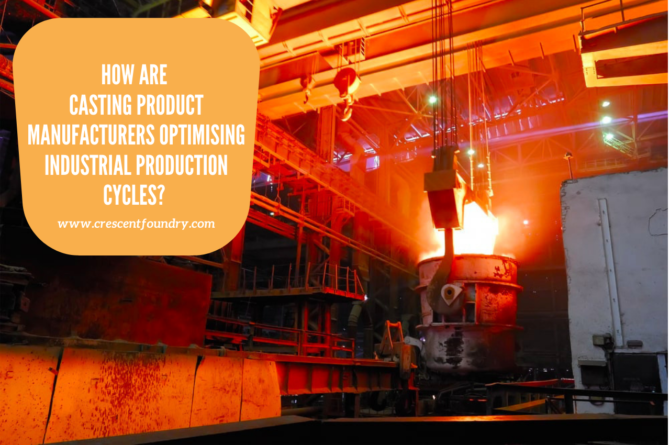
How Are Casting Product Manufacturers Optimising Industrial Production Cycles?
The global foundry sector is constantly growing smarter and more efficient. Leading casting products manufacturers are making the best possible usage of the ever-evolving technology, ensuring that the manufacturing processes are proactive, industrial production cycles are more productive, and the benefits of Industry 4.0 are attained. In what follows, we will take a look at how casting manufacturers are helping in making production cycles more efficient than ever before:
By Supplying A Wide Range Of Products
The best casting product manufacturer companies generally have a wide variety of premium-grade products in their portfolio. As such, they can cater to the diverse requirements of different clients with ease. Customized designs are made, and all possible restrictions related to thickness, shape or size are eliminated. Relatively complex shapes like propellers, valves, and engine cylinders can be manufactured seamlessly – and due care is taken to ensure that the turnaround times are quick. Further flexibility is added to casting processes by the fact that most metals and alloys (apart from high-quality iron) can be easily used as casting material. Scrap materials and waste products can be easily recycled, minimising the burden on the environment. Compared to forging, power consumption is significantly lower in casting as well. Since casting processes deliver excellent consistency, they are ideally suited for varying scales of production.
By Ensuring Flexibility In Production Capacities
Leading foundries play an important role in making industrial production cycles more flexible, by altering their production capacities as per precise buyer requirements. Fully safe and agile production methodologies are followed by the in-house teams – and tooling expenses (along with unit costs) are managed expertly so that the overall costs of production do not become exorbitant. There are powerful fabrication units that can design and deliver customized fabricated products and pallets. Depending on the customer requirements, top casting products manufacturers can vary their production capacities from as low as 200 pieces per year to well over 100,000 pieces per year. These companies specialize in delivering end-to-end machining solutions to customers, ensuring optimal buyer satisfaction.
By Focusing On Precision And Accuracy
The ability to manufacture and supply top-class casting products with close mechanical tolerance is something that makes the best casting product manufacturer companies stand out. Since the dimensional fluctuations from one product to another is minimal, mechanical accuracy can be maintained at high levels. For achieving comparatively complicated shapes, casting is by far the most economical option – and that, in turn, translates to considerable customer savings as well. Enhanced longevity of the products is yet another high point, with casting tools having minimal mechanical fatigue and high corrosion resistance. As a result, there is no need for frequent repairs/replacements either. Since the cooling rates are low, the uniformity of casting properties is maintained. Thanks to these advantages, casting is increasingly finding usage in practically all sectors – right from automotive and construction, to waterworks, railways, agriculture, and industrial applications. Broadly speaking, technological advancements are being instrumental in expanding the usability of casting products.
Casting Products Manufacturers Deliver Top-Class Surface Finishes
The fine finishes of casting products manufactured by leading suppliers ensure superior usability. These smooth surface finishes allow customers to use these foundry products with different metallic surfaces and a wide range of other applications. In most cases, there is no requirement for further polishing either, since the original finishing is typically clean and shiny. If needed, castings can also be painted, coated, plated, and/or customized in other ways. Unit costs are minimized, while additional tooling requirements are kept low as well. The internal teams at the foundries are highly experienced, and they have the knowledge to deliver the best results. The industrial production cycles are made economical and efficient, ensuring that customers can purchase the casting tools they need at competitive rates.
By Minimising Additional Machining Requirements
Elimination of secondary machining is yet another way in which leading manufacturers and exporters of casting products add value to industrial production cycles. The time and monetary savings are both significant (and total costs do not spiral upwards), and there are no unnecessary mechanical hassles either. Close dimensional control, smooth finishing and easy repeatability are among the biggest advantages of the casting process workflows. Manufacturers also create permanent molds based on the requirements and preferences of their clients. The latest technology can be implemented in the state-of-the-art physical, chemical, and paint laboratories of the casting product manufacturer companies – so that casting products of the finest quality can be obtained. The companies are committed to continuously improving their service lines – so that buyers can get higher ROI.
By Providing Operational Integrity and Reliability
For the best casting product manufacturer firms, the focus is squarely on prioritizing the requirements of their clients and delivering products accordingly. Their operations offer an ideal combination of excellent business ethics and professional expertise – boosting overall reliability. Many leading companies also have prestigious professional certifications, underlying their service excellence. For example, Crescent Foundry has the ISO 9001:2015, ISO 14001:2015, and OHSAS 18001:2015 certifications. The leading foundries make use of high-performance cupolas and induction furnaces, ensuring top-class melting capacities. The manufacturing facilities of these companies are also world-class, and generally include CNC-based systems, SAP integrations, hand molding tools, and other necessary equipment. Premium-quality ductile iron/grey iron is commonly used as the casting material – and producers also share all requisite information to customers, so that the latter can get the maximum value from the casting products.
By Manufacturing Castings of Complex Shapes and High Quality
From counterweights to manhole covers, and from agricultural foundry applications to industrial tools, casting product suppliers design a diverse array of high-quality casting products. These manufactured products can be of different shapes, based on the exact project needs and/or customer specifications. The latest molding, coring, and overall manufacturing standards are followed, to ensure the ready availability of glitch-free products. International quality parameters are adhered to, through stringent process control, regular testing, and expert engineering procedures. All stages of casting product manufacturing are constantly monitored, and tooling developments are carefully handled by the teams. Mechanical wear and tear is minimal, and the casting products are custom-designed to deliver the desired functionality.
Across the world, technological innovations are driving the metal casting industry – with both product quality and usability receiving big boosts, and production cycles becoming increasingly optimized. Leading casting products manufacturers typically have a robust skill and professional knowledge base – so that operations are highly innovative and flexible. The demand for reliable casting manufacturers is expected to grow exponentially in the foreseeable future – and companies are geared up to meet this challenge.